PCB Substrate Designs
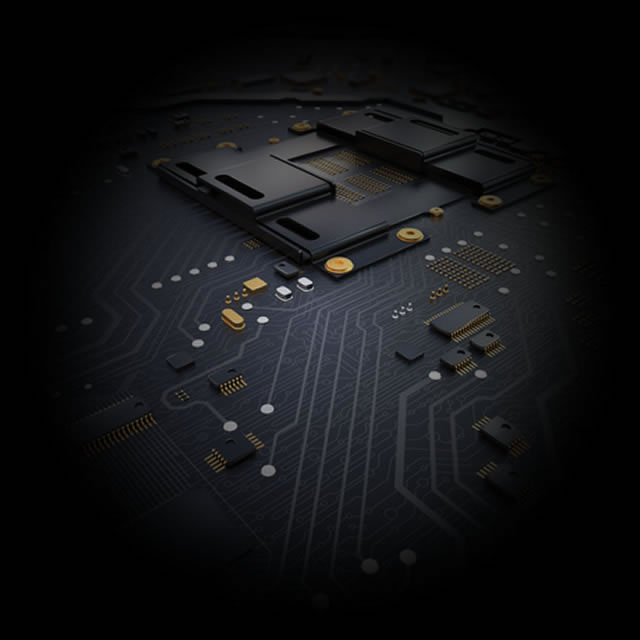
TinyPCB Miniaturization
TinyPCB Inc., American design house and miniaturization partner, providing novel PCB designs and proprietary solutions for Semiconductor Packaging Industry.
Our mission is to break the technology barriers for higher density distribution challenges and to minimize the gap between Wafer / Chip technologies and the PCB / Substrate infrastructure for an optimized multi packaging design.
With 32 US, 32 EU and 32 UK granted patents on modular designs we offer innovative solutions for semiconductor packaging integration which is necessary for the future miniaturization in board level systems.
Our proprietary modular designs and novel solutions will enable hardware developers to innovate faster while also reducing the cost and time to market.